Martin and Susie Hann
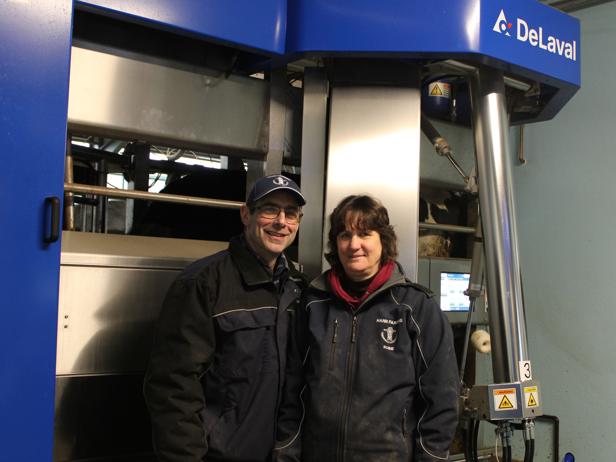
Martin and Susie Hann
Farm location
Somerset, England
Herd size
200
"We’re not tied to the parlour, the robots have effectively doubled the milking workforce whilst freeing us up to focus on other ongoing challenges such as cow health,”
Having moved to a robotic milking system a Somerset dairy farm is seeing increased fertility and higher milk yields. The average milk yield has increased from 28.8 to 30.9 kilos per day. However, there are wider benefits including reduced mastitis and ketosis. The new system is also helping with heat detection, which has improved from 44 to 78 percent since it was installed in October 2019
The couple and their 22 year old son Ryan, supported by Martin’s parents Bernard and Pauline, recently invested in a new shed which has been divided in to four quarters, each with a DeLaval milking robot, robotic scraper and two swinging cow brushes. Two OptiDuo feed pushers run each side of the outward facing feed passages.
“We want to increase the herd size to 240 milking cows,” says Martin. “We looked at a wide variety of dairy farms that use robots and, because we graze our cows in summer, we chose a milk first guided system. This way, when the cows come in to be milked they are not distracted by the TMR which speeds up the milking process,” explains Susie.
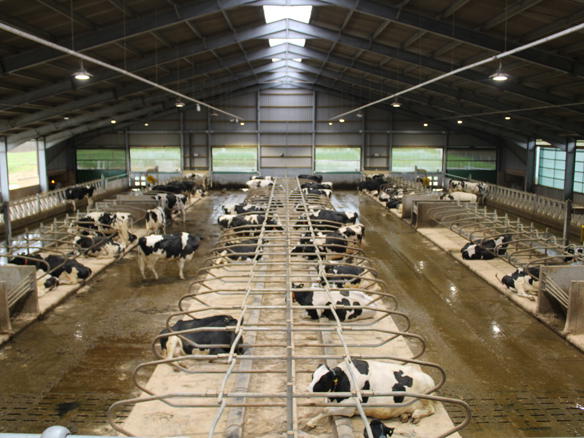
Though still in its infancy, the system is proving a giant leap forward for the farm. “We were milking in a ten unit automatic tandem parlour that was installed in 1993. I still think it’s the best conventional parlour you can use but our cows were quite literally out growing it, some had outgrown the cubicles,” says Martin. The switch took place in 2019. “We brought the cows up in March and started milking on 9th April,” says Martin.
Herd Navigator
A herd monitoring system, provides data on cow health by testing milk samples. “We load cassettes of sample sticks that the system uses to collect and test milk from each cow individually. The data is fed into the DelPro management system which gives us information about every cow,” Susie explains. The Hanns have previously showed cows, so cow health has always been of paramount concern.
The transition to robots was chosen to integrate the technology in a way that would allow the family more time to focus on and improve cow health and fertility. “It seemed obvious to give the cows the opportunity to be milked more than twice a day. Why make them wait twelve hours? This coupled with the advantages of the management system and Herd Navigator to give us data about every cow daily made moving to robots an obvious progression for the farm,” says Martin.
The utilisation of Herd Navigator extends to mastitis and ketosis management, urea monitoring, and most importantly it helps the Hanns manage fertility. “Progesterone levels are detected from milk samples that are fed into Herd Navigator from the robots. We discovered we were serving too early in the cycle but with this system we can accurately identify a cow in heat at the optimum time,” says Susie.
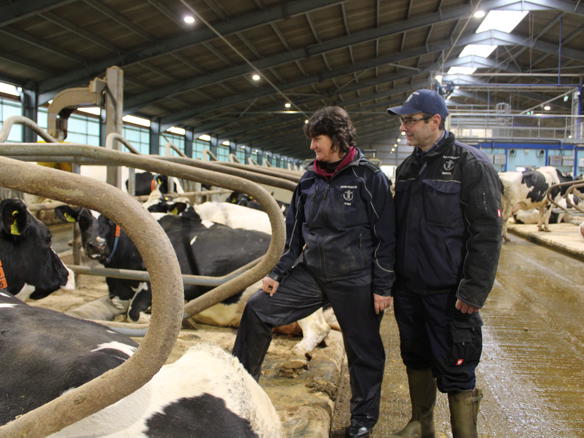
The Hanns are now identifying cows that are not cycling more quickly. “The hormone monitor in Herd Navigator shows us when hormone levels flatline. It also picks up a rise in hormone levels straight away. We would wait 52 days after calving to begin observing when we could serve a cow again. It could be days or weeks for signs of bulling, but with Herd Navigator we can see a change on day 53 and act immediately,” says Martin. The Hanns can export data or send screen shots to their vet, Richard Talbot of Garston Vets. Mr Talbot now makes fewer visits to the farm and rarely performs PD tests which is saving the farm money and allowing him to focus on other herd health issues.
Though time consuming, milking in a traditional parlour allowed the Hanns to monitor mastitis daily. “When you are there you know when there is a problem,” says Martin. However, the robotic system provides a report listing potential cases. “It’s based on a probability score and we check every report cow with either a score over fifty percent or a rising trend The system can’t tell the difference between clinical and sub-clinical, but it picks up the signs of mastitis much earlier than we could manually. This reduces the length of treatment, saves us time and helps prevent milk losses,” says Martin.
The data collected, and the time saved by not being in the parlour milking, has changed the way the Hanns monitor the herd and is offering levels of insight they would otherwise not have been able to achieve. “We’re not tied to the parlour, the robots have effectively doubled the milking workforce whilst freeing us up to focus on other ongoing challenges such as cow health,” says Martin. “We have a herdsman and an apprentice, so we keep our overheads down and avoid the tricky management of recruitment,” he adds.
The Hanns have not chosen robots based on milk yield or automation. Instead, the technology has created an entirely new farming method based on data analysis and hard facts rather than gut instincts and observations. “Robots don’t directly lift milk yield, but they do free up six hours of the day to monitor cow health. This means the cows are under less stress which lifts the milk. Everyone we know who has a robot has seen a lift in milk yield but we think it is because the robot becomes part of the team and allows us, the farmer, to spend our time improving cow health which improves yield,” concludes Martin.